Building the Framework of the car (pun intended)
- gonzagabajasae
- Apr 16, 2019
- 2 min read
In the last 3 cars we have built, we have had a common theme of running a strong, but overbuilt (and overly heavy) frame of the car. This has allowed us to remove the concern of damaging the frame while driving, so that we can focus on more dynamic components of the car, such as suspension, steering, braking, drivetrain, etc. Since we have been a small team, and are relatively novice compared to our competition (5 years of events versus 20+ years), we have had to focus our efforts yearly on what requires more growth.
This year is the year where we are finally putting all of our best designs into one, which means we should give it the best frame possible. This was our main thought process around why we designed the frame so radically different than years prior.
In the image below, you will see our previous car, named HR3 (short for Holy Roller 3). In this photo, you can see we are running an A pillar and B pillar style cabin, as well as triangulated side impact members along the body of the car. You will also notice there are a lot of bent tubes, which requires a larger tubing wall thickness (.065" vs .035") for secondary members, and adds length and weight to primary tubing members.
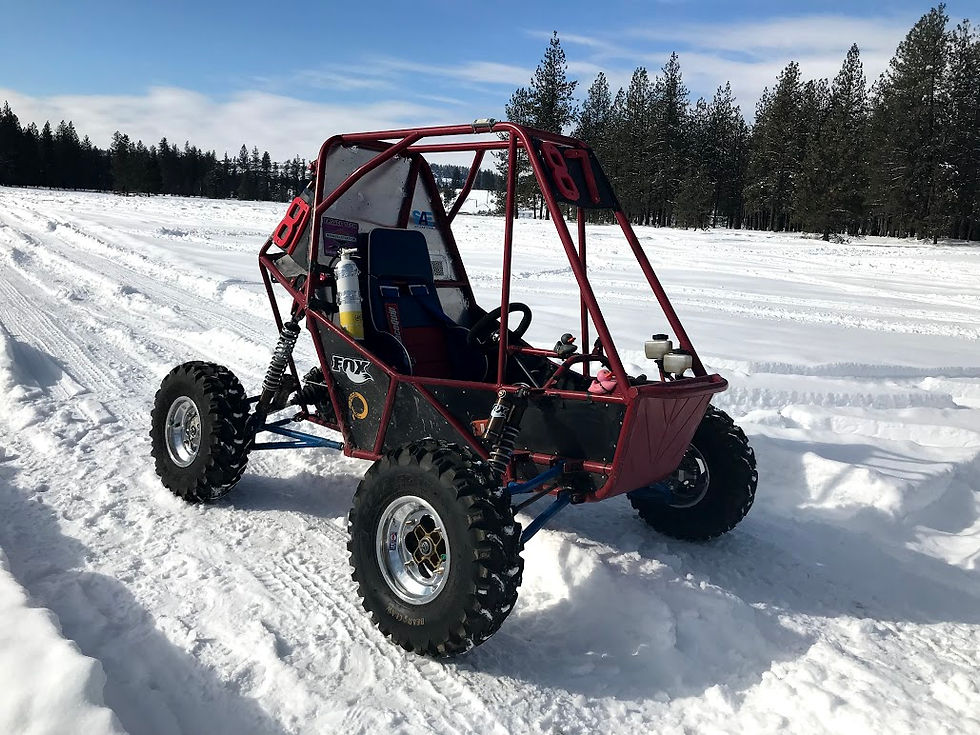
In the photo below, you can see the upcoming HR4 frame. With a deeper analysis of the rules, and adjustments of our frame design, we were able to remove the need for A and B pillars, as well as those triangulated side members, greatly reducing the weight of the main frame body. This was achieved by removing the bends in the primary side members, narrowing the tub of the car, and utilizing a rear support member for chassis rigidity. Even though the car is narrower, with the newly designed side members and seat position, there is actually more in cabin space.

As the build season has progressed, components such as the firewall and belly pan have been constructed. The main difference with these being that the firewall will now be mounted on the front side of the passenger cabin, and the belly pan is made out of light weight aluminum sheet, with added strips for rigidity.
This year, we have also continued our work with carbon composites, namely Carbon Fiber for protective side panels of the car, as well as a rear belly pan for the engine area.
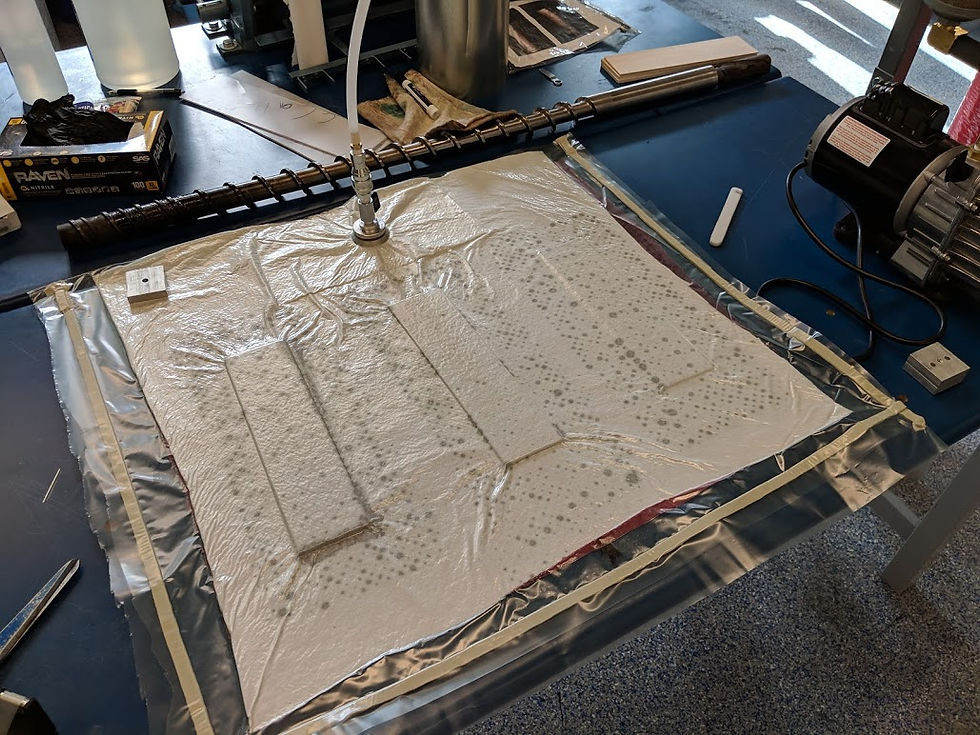
We tested 3 different styles of construction for our carbon fiber belly pan. All 3 were six sheets thick, but varied from having 1/8" to 1/4" balsa wood strips laid between the layers for added rigidity.
Our testing showed that the sheets with a single 1/8" balsa wood strip were the best combination of rigidity, form factor, and weight.
As final tabs and mounting brackets have been installed, the final touches for the frame were nearly done. The last thing to do now, is decide what color to choose to paint it?
After some deliberation, we settled on Petty Blue (or Dynaco blue for all those Cars fans out there) with white suspension components. We think it turned out pretty good, and it will definitely make the car easy to spot out on the track!

Comments